The Ultimate Multi-Container Build Guide
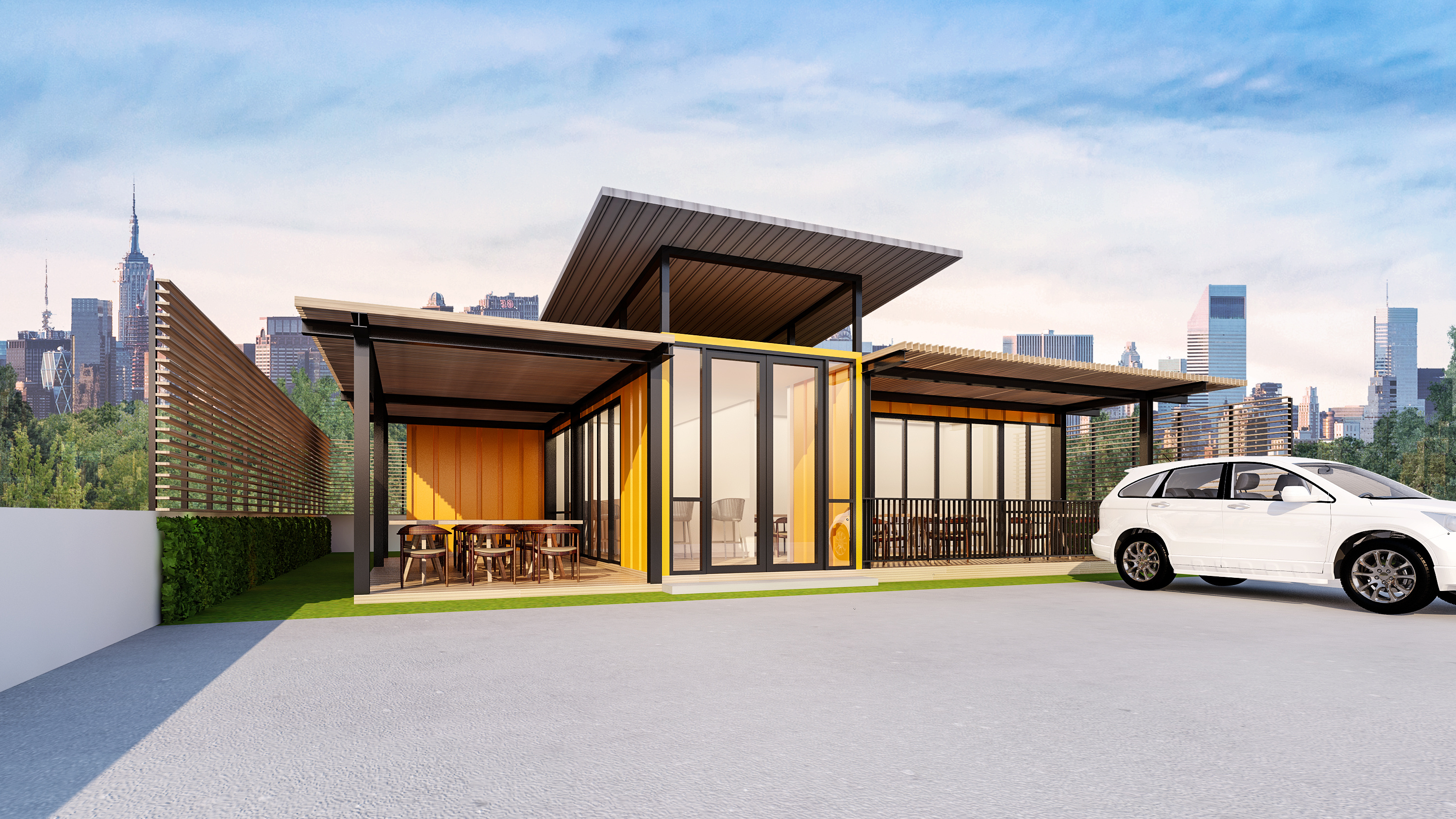
That Doesn’t Break the Bank...
As humans in the age of tech and social media, content is everywhere. Whether it be filtered pictures on Instagram, creative TikToks, or a website, our lives are filled with creative content. As customizers of shipping containers we receive a lot of questions, but one we see a lot is “How much would it take to build this?”. We are then handed a napkin drawing or an image of a 3,600-square-foot container home. These kinds of projects are truly awe-inspiring, but they are also created to do just that, inspire awe. Taking some time to understand all that has gone into that shipping container build can help you understand what kind of undertaking a similar project would be. In this guide, you will explore the more cost-effective options in putting multiple containers together and learn more about the processes that lead to an increase in cost so you can build the container of your dreams and also within your budget.
On-Site Work
Shipping container homes and other structures utilize steel, so if you are looking to put two or more together, you’re going to have to hire a welder. This, along with a few other tasks related to your build, all apply to work being done at the location of your soon-to-be home.
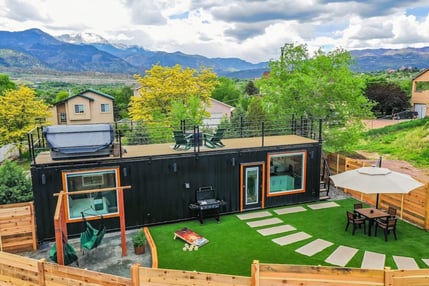
Welders, depending on many factors, can get pretty pricey when looking at linear feet of welding. Picture the difference between welding one doorway together to connect a container (about 20 linear feet) and welding 6 containers together at multiple points. You could be welding hundreds of linear feet together and could end up costing more than the containers themselves.
While there are many other forms of on-site work, welding is by far the most expensive. If you approach your multi-unit container build with the mentality of keeping on-site work to an absolute minimum, you will keep your costs down and you can have your home delivered and able to be lived in much more quickly. We deliver fabricated modules that need to be assembled on location. Consider the heavy machinery required for placing the containers in their final location. The units can weigh more than 10,000 pounds and typically require either a fork-lift or crane to move. If you choose to stack containers on top of one another you will need, at the very least, a modest forklift, and, at the very most, an on-site crane to maneuver and place your containers.
Making Cuts into the Container
Every time you make cuts into the sides of containers you're breaking the structural integrity of the container. Once a cut has been made, you have to reinforce what was removed. By cutting more area out of the sides or top of the shipping container you are introducing the need for more support and stability needed to maintain the structural integrity of the unit. This leads to more on-site work in welding and fitting the two containers together. Now let’s talk about a few of the best ways to keep those costs down, which is the whole purpose of buying a shipping container!
Cost-Effective Build Styles
Below you will find four of the most effective ways to build a multi-unit container home. These have the intention to keep costs as low as possible by keeping cutting and welding to a minimum.
We have experience building all four options, so if you like the idea of one of these, be sure to reach out and chat with one of our container techs today. These builds could easily still climb well into 6 figures depending on how you want them built out, but this should give you a decent idea of what to expect with each and we can talk about how to build them out further. We make it a point to keep you from making a bad decision.
L-Shape or T-Shape Container Build
Unconnected L-shape or T-shape Container
If you take two containers, no matter the size, and place them *next* to one another, but not connected, it would be the most cost-effective way to increase livable square footage in your container home. While there is a little bit more that goes into planning out your area for delivery, you can just about take the cost of two container homes you like on the site and we can place them wherever you would like them. Many folks take a deck to connect them and make them look and feel like a conjoined unit, but they really are just placed next to one another. This is by far the most cost-effective option.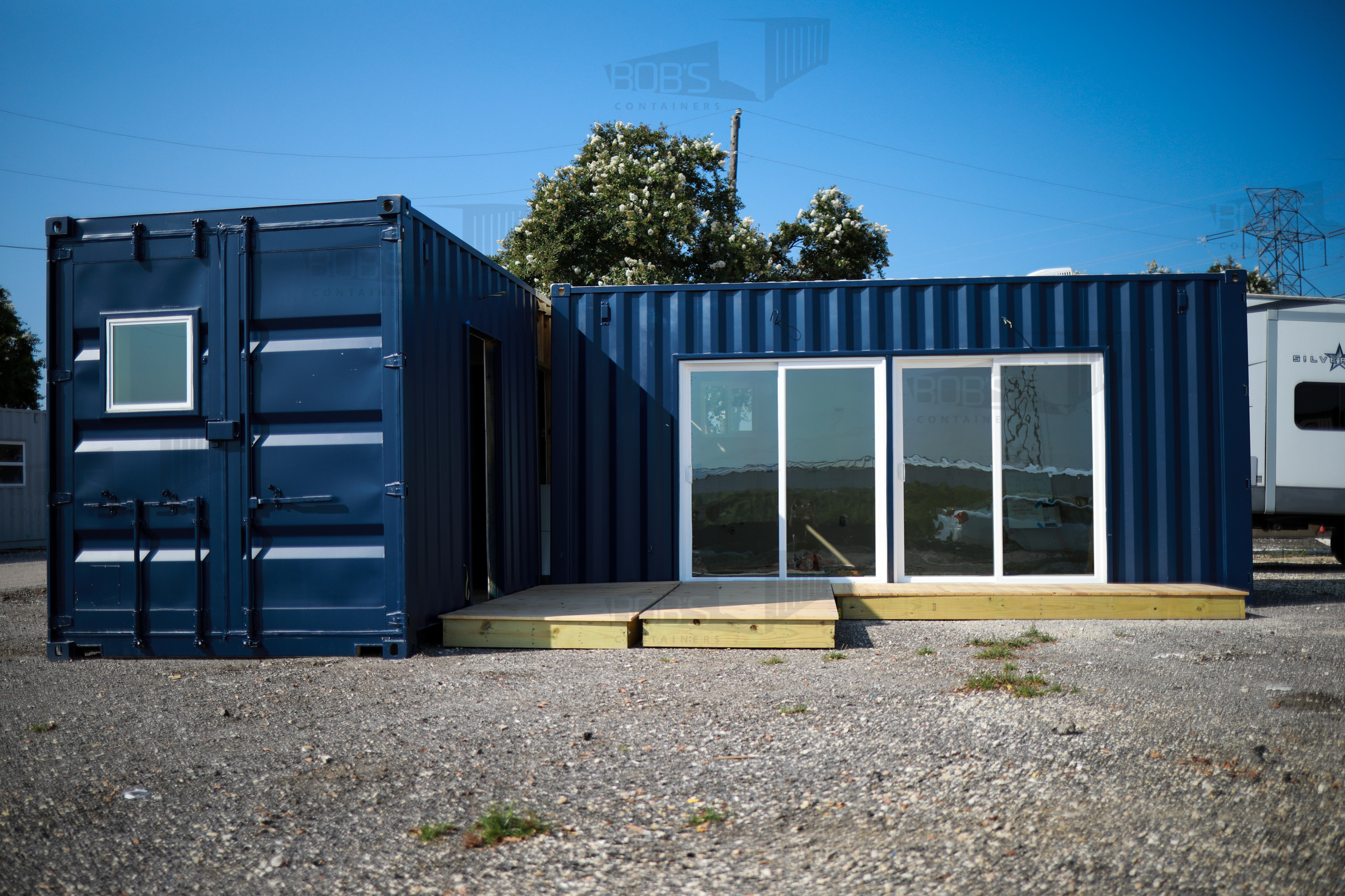
Connected L-shape or T-shape Container
Once we introduce cuts and welding, the build and delivery become more tricky as we have to consider on-site work. We can execute the majority of the build at our shop, but there is no way to get around the cost of welding unless you have the ability yourself. Consider the difference in one end of one container being completely removed and a hole having to be cut in the side of a container where the two containers will join, versus a small cut the size of a door in the same space. On top of this with the build with more cuts, a large portion of the side has been cut and therefore has to be reinforced to keep the structural integrity. We would not recommend this type of build if you are trying to keep costs down. Keeping the sides of the container intact keeps the on-site work to a minimum as we can make both of the cuts and prepare the unit for delivery, leaving a few linear feet of welding as long as everything else falls where it should. The model pictured above gives you over 300 square feet of livable space out of two shipping containers! Place a deck and a cover over the area in between and you are going to be wondering why you had not thought of this years ago.
Atrium Style
Another great option to combine shipping containers and increase your square footage is to take two (or more) containers and place them some distance apart with the intention of developing the space between the two containers into a livable area. This lends itself to some creativity, but keep in mind that creativity is what can increase costs quickly.
As long as you keep those cuts in between to a minimum, you’ll be just fine. Blowing out two entire walls and welding them together will have your costs balloon to where it may not even make sense to build using shipping containers.
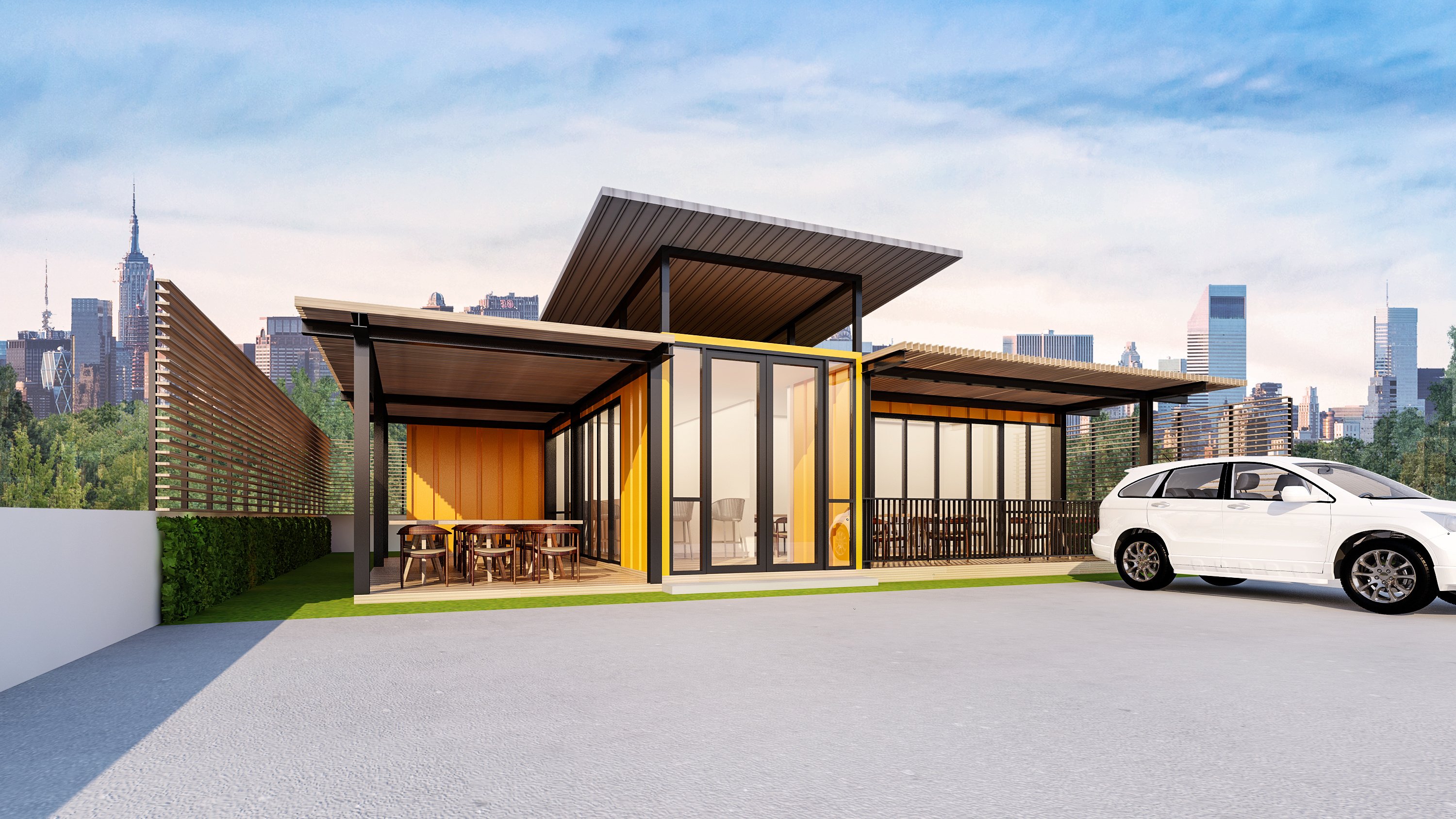
Stacked Container Home
Stacking containers to create a home is a great way to increase your living space vertically if your plot has less area. You will likely always use a bigger container on the bottom as the base and use a smaller container up top if you should decide to use two different-sized containers. Connecting a roof to a floor is not too intensive on on-site work, so you keep linear feet of welding down, but you will have to maneuver and place the container with a crane or forklift which can pose its own set of challenges.
If you pair this with solar/off-grid options, you can have a very small carbon footprint along with your stacked home. These are excellent options for AirBnBs and In-law suites as well. This type of build removes none of the structural stability of the container, so, rest assured, that your home will withstand just about anything you throw at it.
Double or Triple Wide (Side by Side)
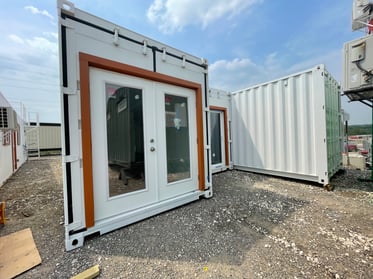
A double or triple-wide container home, much like a stacked container home, utilizes the structural integrity of each container well as long as you do not cut entire walls down in between. Once you start taking out large portions of steel wall, you have to consider supporting the structure. Keep your cuts to about the size of a door and you will limit the amount of on-site work needed to complete the build. These, much like the rest, can be built at our shop and delivered to be put together. Another benefit of putting containers next to one another is the opportunity for more space above the container for something like a deck as pictured here.
Multi-Unit Builds as Art Pieces
As you browse for inspiration, be sure to consider what the use of the property may be for. Many times we see developers create completely off-the-wall builds as a sort of ad for their business. While these catch your eye to draw you in, the reality is these types of builds can cost exponentially more than a traditional stick-and-frame home. As we have talked about throughout this guide, the greater majority of what these kinds of builds need is on-site work. The containers are only the beginning in builds like these, the planning, engineering, and development that has to be worked through before putting a cutting wheel to steel or a welder to a joint can be astronomical.
Starting From Scratch
When you have a grand idea, do consider the amount of work that will go into the development, creation, and delivery of your dream container. Part of what makes us who we are and keeps our prices so low is we have gone through the architectural and engineering process to know what works and what does not. When you bring a napkin drawing or a picture from Google to the fold, we start that process from zero. Introducing cuts and connections within multiple containers complicates that process quickly, and we have not even taken a cutting disc to some steel yet.
A Few Rules to Follow
If you’re into this kind of thing, a few rules to follow can help you start off on the right foot with a multi-container build if you are looking to save some cost.
If none of the below matters to you and you’re dead set on your napkin drawing, schedule a meeting with a container tech.
We can certainly make all of your wildest dreams come to life. If you are trying to stay on the more conservative side, try to keep these rules in mind.
- Keep on-site work to a minimum (welding or heavy equipment for stacking containers)
- Keep the number of cuts to a minimum (windows, doors, and connection points)
- Keep the size of the cuts to a minimum and do not exceed 72 inches wide and leave at least 24 inches from the ceiling to the top of the cut (if doing floor-to-ceiling cuts) Take advantage of our pre-designed units and find units that will match together naturally
- Do not plan to blow out entire sides of your containers as engineering costs can skyrocket quickly.
- Consider joining the two containers with either decking or an atrium-style build combining containers and traditional wood structures.
Taking the time to consider not just the look and feel, but the development required for execution has been the theme throughout, but it can be tough to navigate when you do not really know what you are up against. If you are still interested in building a multi-unit container home, schedule a meeting with one of our container techs today. We look forward to building your dreams.
Building with Bob’s
With Bob’s Containers build process, you are able to see the progress of your build and know that what you are going to have delivered on delivery day is up to standard. That process goes for our single container builds or multi-unit build like you may be considering now.
Our build team is a team of experts who not only know shipping containers, but know construction through and through. When you build with us, you know the finer details will be executed with precision. It is those finer details that can really bring a shipping container home to life. Whether we are looking at the black eggshell finish on our Joshua Model, or the simplistic elegance of The Kerrville, those are the finer details that can make your container feel like home.